This website uses cookies to ensure you get the best experience on our website. Read more
Lost Wax Process In Gemstone Jewelry Manufacturing
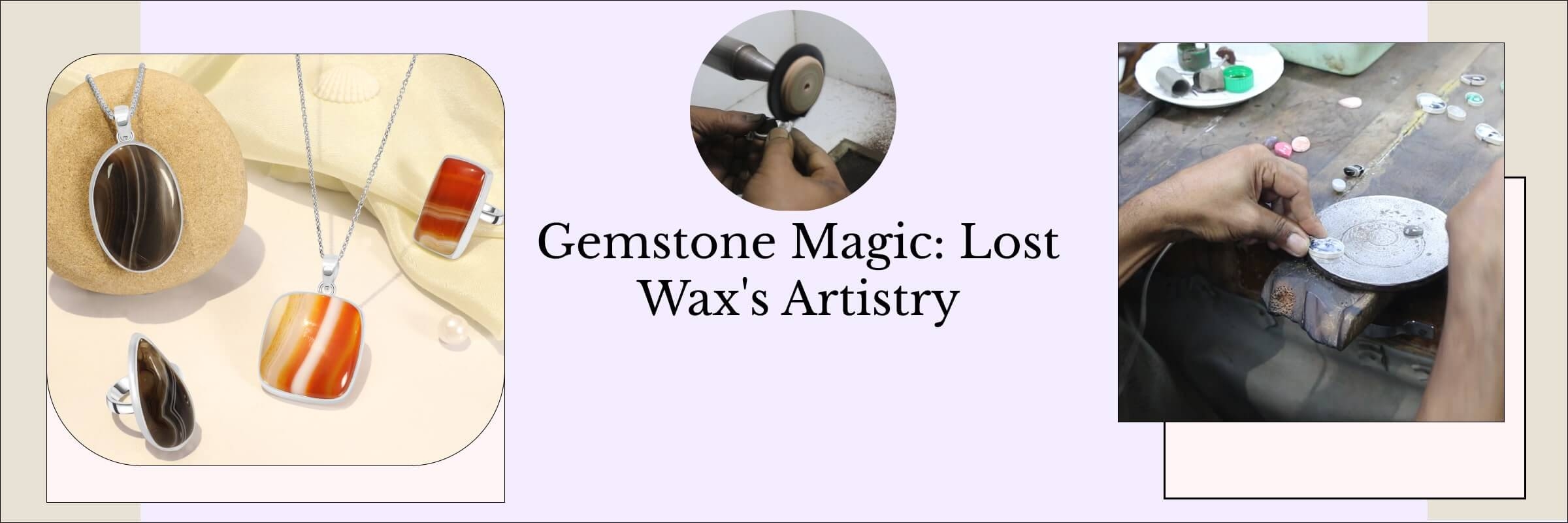
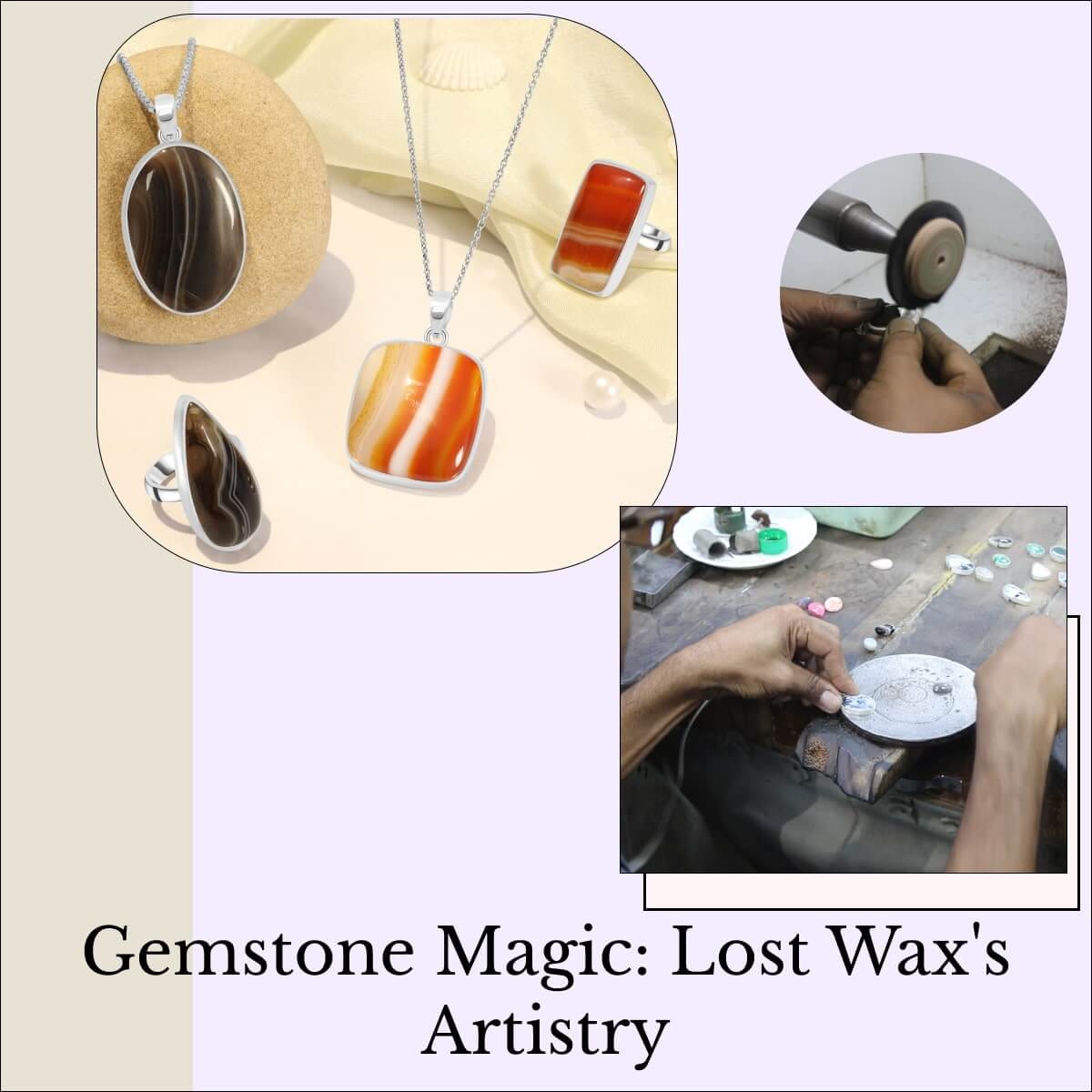
Overview
The technique of Lost Wax Casting, which is popular right now, has been used to make amazing jewelry. It is one of the widely utilized methods for creating exquisite works of metal art. Lost Wax Casting, also known as "investment casting" or "precision casting," was the most popular type of metal casting until the 18th century, when piece moulding—a production technique that involves combining individual components made from numerous different casts—became increasingly prevalent. Great Gemstone Jewelry is produced using this way of manufacturing. The labor-intensive lost wax process entails many steps. The oldest known things created using this technique date back to jewelry from the Indus Valley Civilization of South Asia and artifacts from Nahal Mishmar. This type of metalworking has been practiced for thousands of years.
In the conventional lost wax technique, a wax model is used to manufacture a metal object. This association also goes by the name of venture projecting, a 6,000-year-old strategy. Lost Wax Casting, which can swiftly and precisely produce complicated patterns, is still frequently utilized in the jewelry industry even though piece moulding is preferred for the production of larger metalworks. Over the centuries, the procedure has undergone a few minor alterations, but for the most part, the processes required to create a lost wax cast have stayed the same:
Wax Model
A model of the desired product is created first. The model would be cut from wax and moved directly to the next stage if it was intended for a single-use casting. When creating Gemstone Jewelry designs that include set gemstones, the desired stone is frequently set straight into the wax blank and the setting is carved into shape around it before being removed to achieve a tight fit in the final jewelry item. For mass production, the original model may be carved from wax or another rigid but pliable material, like clay, before being turned into a mould to produce numerous wax copies.
The copies made from a mould frequently have a hollow core to improve wax flow during the casting process' "burnout" step and frequently need to be "chased" after being removed from the mould, which entails smoothing out areas on the model where the mould left a mark. In the contemporary era, wax models are sometimes obtained by first being sculpted with computer aided design before being rendered by a 3D printer in wax, or if the model is to be used as the base for a mould it will be 3D printed in resin.
Wax Model Spruing
The generated model is known as a sprued if the aforementioned phase has been completed and the intended result has been achieved. This stage entails fastening numerous wax supports to various points on the model, which, when finished, frequently resembles the shape of a tree. These additional wax supports create hollow channels within the shell that are used to create the final metal cast, allowing metal to flow freely throughout the shell. Typically, these hollow channels are orientated in the same direction as the model as a whole.
Investment
The wax figure is then covered with a layer of a substance known as a slurry. This coating may be made of other heat-resistant materials, but often it is a type of ceramic that is enclosed around the wax model layer by layer, frequently by dipping the model. Investment is the term used to describe this stage of the Lost Wax Process. The process of coating the wax model with slurry is another name for it.
Burnout of The Slurried Model
The wax model is fully encased after which the shell is hardened. This process is called "burnout," and it involves heating the wax model upside down in a furnace or kiln until it melts and flows out of the shell. A support is sometimes employed to hold the slurry shell upright while it is heated, while in other instances a flat surface is cut into the top of the slurry after it has hardened to permit being inverted while this process is taking place.
What remains after the burnout step is a specialised mould which can withstand the stress of contact with molten metal but also contains a highly precise impression of the original model. At this stage the shell is often tested with water to ensure that it has no cracks but also allows fluids to freely flow within it. This needs great attention and should be performed with care.
Pouring the Cast Material
The next step is to pour the cast material once the wax model has been burned. The wax model is burned out of its shell, and then metal is poured into the channels the wax sprues left behind. The Lost Wax Process must be done while the solidified slurry is still hot to prevent cracking due to temperature variations between it and molten metal. The next step is to let it cool after you've finished.
The Solidified Cast is Released
In this process of the Lost Wax Process fresh cast is expelled from its container once it has fully hardened. In order to release the cast, the casting shell must typically be completely destroyed, which may require the use of chisels, hammers, or sandblasters.
Complete Step
After being released, the finished cast is next pursued to remove surface flaws before being cut free from the metal rods that the sprue channels had left behind. The cast can be used right away after being chased or sent somewhere for additional finishing, including painting, stone setting, or enamelling.
Conclusion
One of the most popular processes for making Gemstone jewelry is the Lost Wax Process. This allows for the creation of distinctive jewelry designs with excellent precision. Precision and accuracy are necessary for the creation of jewelry. People adore Gemstone Jewelry, Casting Jewelry, Custom Jewelry, and Alphabet Jewelry. At Rananjay Exports, a reputable Wholesale Gemstone Jewelry Manufacturer And Supplier, you may buy genuine Gemstone Jewelry or the attractive Sterling Silver Jewelry.